EV Integration and Testing
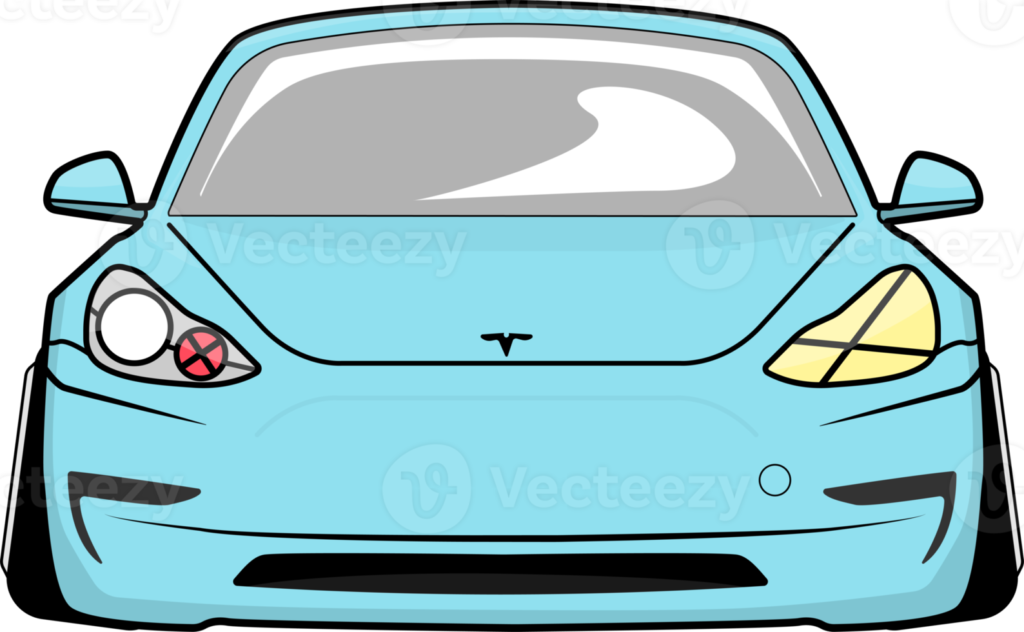
The above two components such as EVPT and EVESS will be integrated into the already developed EV prototype at the School of Mechanical and Manufacturing Engineering (SMME), NUST which is at the forefront of research in sustainable energy.
In this context, we have successfully developed functional prototypes for electric cars and bikes which are being tested on campus to shuttle between faculties and departments. The school also has a state-of-the-art manufacturing facility that has CNC machines and a material resource center for conventional manufacturing and fabrication. Already Prof. Dr. Imran, the co-PI from SMME has extensive experience in the fields of design and manufacturing, particularly machining, welding, and the use of design software (ProE/Creo and Solidworks).
He brings with him over 5-year industrial experience, especially in the design and integration of aerospace vehicle systems and has also carried out research relevant to this project, especially in the field of design and manufacturing, as well as the testing and use of PV-based electric vehicle technologies including solar charging stations. This research has already been published in leading international journals of repute as well as international conference
In this project, full-scale electric vehicles will be analyzed and road-tested for the designed ECPT and EVES components. A modular design approach will be adopted for ease of integration, testing, and identification and troubleshooting of errors during lab as well as road testing. Mechanical and structural as well as aerodynamic stability of the carriages and track will simultaneously be carried out. Also, technical validation will be carried out for future commercialization. Overall, the digital design, manufacturing, and assembly of the mechanical systems, and the overall integration of the systems into the EV. The mechanical design will include exterior and interior design using suitable CAD software like ProE/Creo/Solidworks. Effective utilization of modular design theory will be implemented using the design of manufacturing (DfM) and design for assembly (DfA) approaches. After design verification through the virtual model, manufacturing drawings will be generated, and using them, a fully functional prototype will be manufactured. The prototype will be road tested after assembly and integration of electrical systems, power train, and sensors using real-time data acquisition of environmental and performance parameters (battery state, mileage, solar insolation, speed, acceleration, vibrations, energy consumption, etc.)
Project KPIs








