Battery Pack Design with Battery Management System BMS
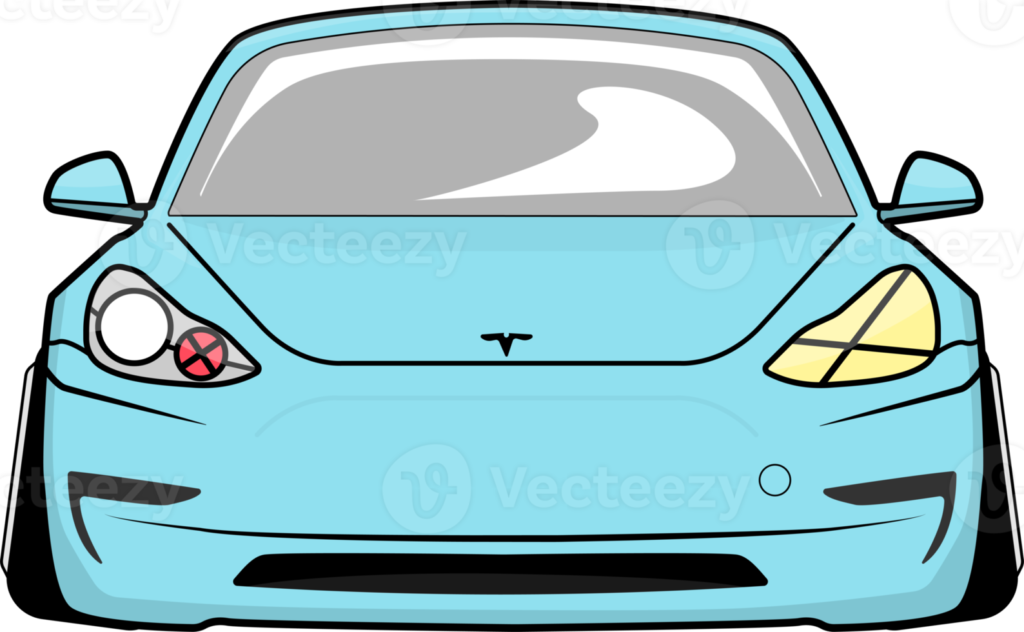
Temperature is one of the major factors that influence performance and SOH directly. Where the ideal operating temperature of the Li-Ion cell is between 15 - 35 °C. The internal resistance and polarization also vary with respect to temperature.
At higher temperatures, the cell degrades rapidly [13]. Fig 3 shows the three stages in battery TR, Ts, safe work temperature (for battery); Te, temperature for people to escape; *SOC dependent. The top level of the Li-ion bill of materials is called the pack. The pack consists of multiple modules joined together, with mechanical fixings which allow for easier disassembly for servicing purposes. The pack also contains a battery management system which also controls the thermal management system of each module. Module assembly is carried out in a similar way to that of unit assembly.
Depending on whether the design requires a series or parallel configuration, module designs position negative and positive terminals on opposing ends or same end of each cell. The cells are therefore joined by tab to tab or tab to bus bar connection. Ultrasonic welding is primarily used for this process as it allows for good quality welds across dissimilar materials and across multiple layers.
The module assembly process is summarized in Fig 4. The process for pack assembly is like that of module assembly. However, to facilitate maintenance and repair, module to module connections is joined using mechanical joining with nuts/bolts or wires. The battery packs are tested, stacked and finally, the modules are connected prior to testing. This process is outlined in Fig 5. The novelty of this project is in its compact design of battery pack for the on-road vehicle, which will bind dozens of the Li-Ion cells together. The design emphasizes lightweight, while incorporating both air and/or liquid based Thermal Management System (TMS) to ensure the SOA of temperature to extend the life. Fig 6 shows the whole chart of joining process of automotive battery pack assembly.
Moreover, to modify the battery pack as required by the selected frame for the R&D of the project, separate investigation for required no. of cells, series and parallel connections, battery modules design, modified battery pack cooling system design, physical protection of the battery pack and thermal runaway design. Whereas the important characteristics of the BMS design include measurement accuracy, reliability, ease of installation and maintenance, and cost. The function of an intelligent BMS is to fully store while charging as well as harvest the stored electrical energy while discharging in the large battery packs. Where the BMS will fully be responsible for various functions such as measurement, management, evaluation, communications, and logging [14]. Active cell balancing methodology will be a key to overcoming the issues of energy loss in case of heat dissipation in the case of passive balancing. The BMS will take care of the SOA of an individual cell to extend the energy usage as well as life. The protection of the Li-Ion cells will also incorporate in a form of switches/relays, in case of any emergency, the switch will operate to cut out charging as well as discharging module from the battery pack, these components are given in Fig. 2. Following are some usual functions that a regular BMS performs.
Cell Monitoring
When charging or discharging, the battery cells need to be always monitored. Any outof-spec situation must be identified and reported along with the triggering of the safety mechanism. There are integrated circuits equipped with cell monitoring algorithms that perform this function. There is a chain of command where the cell monitoring circuit records the cell voltage and temperature and passes on the data to a cell management controller. At this stage, some algorithms are run to calculate the state of charge (SOC) and state of health (SOH).
Diagnostics And Power Optimization
Diagnostics is another important dimension of cell monitoring. It helps the EV BMS to identify and report the error codes and diagnostic info. This data can be used to fix the issue or trigger safety mechanisms. Optimization of battery power is another direct outcome of cell monitoring. While the cell monitoring functionality determines SOC and SOH, the EV battery management system’s job is to keep the SOC and SOH parameters within the specified values. When the battery is charging, the EV battery management system determines how much current can be allowed in the individual cells. During the EV operation when the EV is discharging, the BMS ensures that the voltage level does not get too low by communicating with the motor controller.
Safety of Electric Vehicle
Safety is the primary concern when EV power supply and battery management systems are in the picture. An undetected thermal runaway can cause a major mishap. As mentioned earlier, the BMS captures data such as voltage, temperature, and current to optimize the power. A similar set of data is also utilized for ensuring safety. Standards like ISO 26262 have certain requirements that must be fulfilled to ensure that the BMS is developed as a fail-safe system. Another aspect of safety is the insulation of the vehicle body/chassis from the battery pack to avoid electric shock to vehicle occupants.
Battery Charging Optimization
The battery cells deteriorate over time. An intelligent EV BMS factors in this deterioration that results in changes in battery parameters such as voltage, current, etc. For instance, a battery cell gets slightly damaged by heat and starts getting charged at a lower voltage than the rest of the cells. The battery management system is responsible for identifying this fault and optimizing the charging process so that all cells are charged at the lower voltage. This reduces the stress on the overall battery pack and enhances its life. Of course, the BMS diagnostics will also store this issue as a trouble code so that it is fixed at a later stage. Moreover, oxidation in the battery terminals may lead to a reduction in voltage and the BMS adapts to these changes to extract the best performance from the battery.